CASE STUDY
Tanami Desert Gas Pipeline
Buried Coatings
Project Data
Location | Tanami Desert (NT) |
Asset Owner | AGIT |
Products | Denso S43™/R23™ Butyl Tape System |
Date | 2019 |
Project Details
The Tanami Gas Pipeline is a natural gas pipeline linking Newmont Mining’s Granite and Dead Bullock soak mines between Alice Springs and Tanami in the Tanami Desert, NT. The pipeline route was selected over the possibility of a “Virtual Pipeline” which would have seen over 440km of roadway rebuilt for the purpose of trucking in diesel fuels, however due to the unpredictability of the NT wet season and road closures, a buried 440km natural gas pipeline was not only more economical, but also more reliable.
The NT Government approved the construction of the pipeline in June 2018 where AGIT (Australian Gas Infrastructure Tanami) had already engaged the selected contractor with the construction of the pipeline earlier in 2018. The construction of the project is projected to be worth approximately $US250 million and constructed over a 9 month period between June 2018 and completed by March 2019.
The pipeline is made up of nearly 25,000 x 18 metre lengths of 8” 3LPE coated pipe which was sea freighted into Darwin from Bao Steel in China and then road freighted and dropped at 4 separate lay down yards along the pipeline route.
The selected contractor, with approval from AGIT, selected Denso’s S43 R23 Butyl Tape system for the protection of Field Joints and Denso Bore-Wrap™ for Abrasion Resistance (ARO) of 260 linear meters of pipeline protecting both the factory 3LPE coating and the Denso™ S43 R23 tape System. In June 2018 Field Joint coating materials were supplied in 2 x 40 ft containers which were delivered to Alice Springs where the selected contractor had their own holding yard.
Following mobilisation, clear and grade and the arrival of the material, Pre-production Trials (PPT’s) commenced in June where the selected contractor and Queensland Industrial Coatings (QIC) personnel were trained and accredited in application of both the Denso S43/R23 Tape System using the Premier hand Wrapping machine and the Denso Bore-Wrap system by Denso’s SA/NT business manager David Towns. The PPT was conducted at the commencement of the pipeline some 150km NW from Alice Springs.
QIC, who were engaged by the selected contractor for the application of both FJC and ARO operated with 2 coating crews for the most part of the project averaging nearly 600 FJ’s per day (10.8km). At peak production, 1 crew was able to complete 350 Field Joints in 1 day. Mainline Field Joint Coating was completed by QIC by December 2019. Tie-ins were wrapped by the selected contractor simultaneously to QIC on mainline activities.
Both the selected contractor and QIC were overwhelmed by the performance of the S43 R23 Butyl Tape system, with high productivity rates, minimal repairs to the coatings and lowering in was completed swiftly. The Denso Bore-Wrap ARO system also provided the reassurance that no coating would be damaged through boring which again was very easily applied in the hot NT climate with a moisture cured urethane high fibre content bandage applied and ready for pull through within 30 minutes of application.
The projects final Golden Weld was completed in the middle of January 2019 and the construction completed 5 weeks prior to the proposed March deadline.
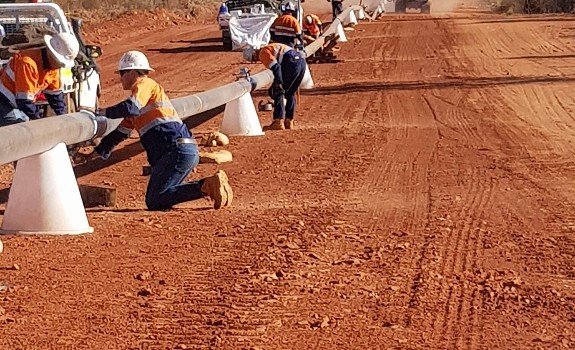
Denso's S43/ R23 Butyl Tape System applied to the Tanami Desert Gas Pipeline.

Denso's S43/ R23 Butyl Tape System applied to the Tanami Desert Gas Pipeline.

Denso's S43/ R23 Butyl Tape System applied to the Tanami Desert Gas Pipeline.

Denso's S43/ R23 Butyl Tape System applied to the Tanami Desert Gas Pipeline.
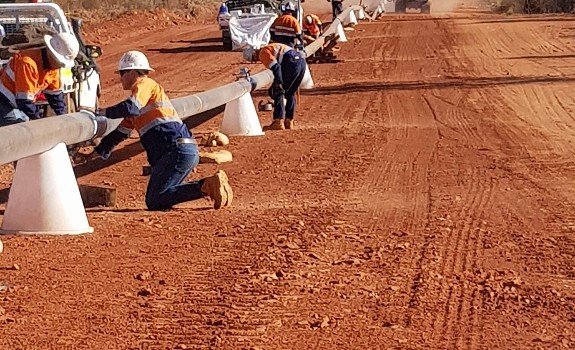
Denso's S43/ R23 Butyl Tape System applied to the Tanami Desert Gas Pipeline.

Denso's S43/ R23 Butyl Tape System applied to the Tanami Desert Gas Pipeline.

Denso's S43/ R23 Butyl Tape System applied to the Tanami Desert Gas Pipeline.
